Researchers pioneer new technique to transform used milk bottles into kayaks and storage tanks
Researchers at Queen’s have discovered new ways to convert single-use plastic waste into products such as storage tanks for water and fuel, and sporting goods such as kayaks and canoes, which could help to solve global environmental problems.
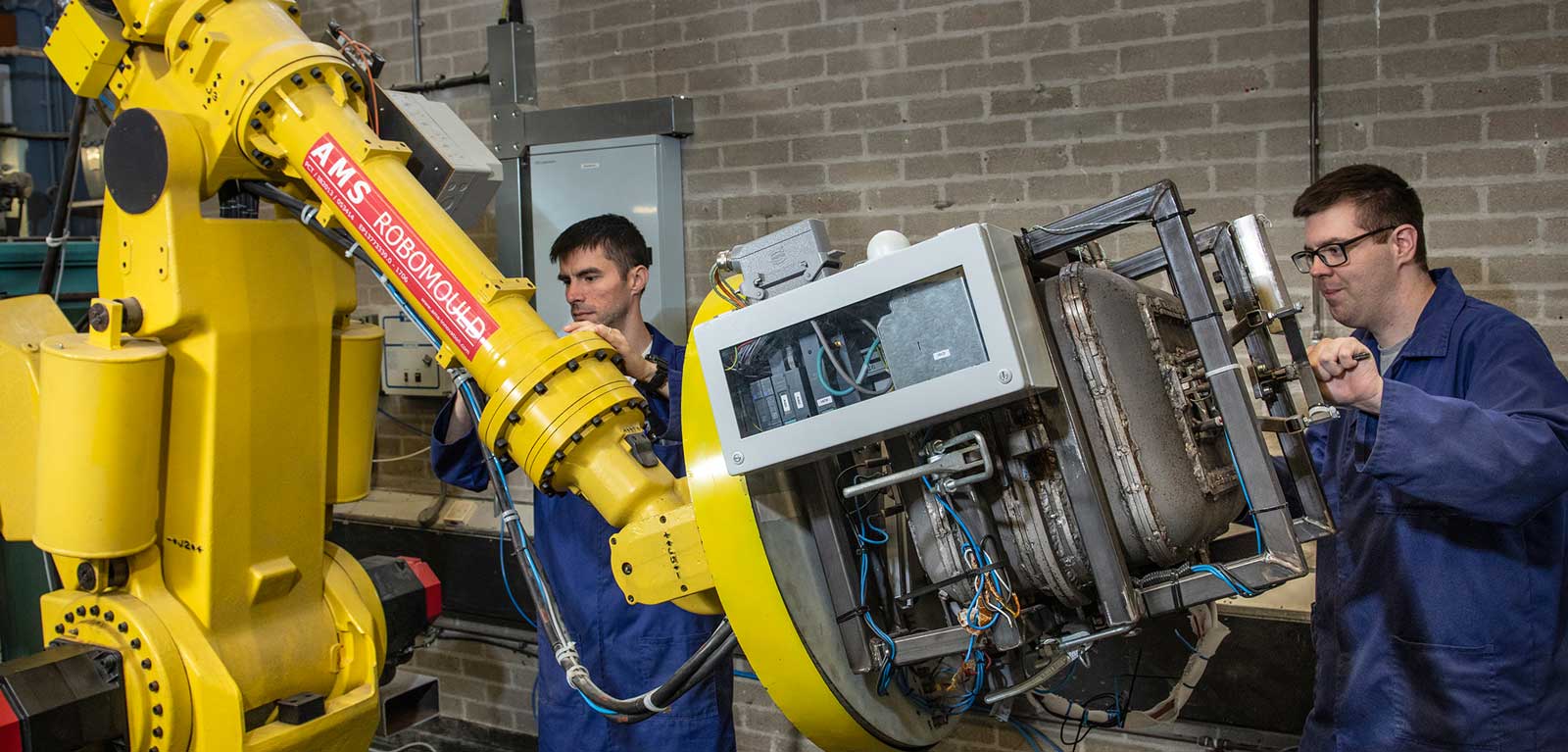
Today the world produces over 300 million tonnes of plastics every year, which is almost equivalent to the weight of the entire human population. Much of this is single-use and not designed to be recycled, which creates a mountain of waste that enters the natural environment such as plastic pollution in the oceans.
However, researchers at the Polymer Processing Research Centre (PPRC) at Queen’s University are pioneering innovative manufacturing techniques to turn waste plastic into a wide variety of useful products.
Their ground-breaking approach involves a manufacturing process called rotational moulding, which has the potential to economically recycle very large volumes of plastic waste into a wide variety of innovative products such as urban street furniture, storage tanks and marine buoys.
The project is funded by Innovate UK through its “Plastics Innovation: Towards Zero Waste” Programme and the researchers are working in collaboration with three industrial partners; Impact Laboratories Ltd in Scotland, Impact Recycling Ltd in England and Harlequin Plastics Ltd in Northern Ireland.
Dr Peter Martin, from the School of Mechanical and Aerospace Engineering at Queen’s, explains: “The Polymer Centre at Queen’s University Belfast has been leading the way in plastics recycling for over 30 years and our engineers are working on novel techniques that could really help to tackle the huge global issue of single-use waste plastics”.
“The process starts with flakes of waste plastics being separated and compounded into pellets using the patented technologies of Impact Laboratories and Impact Recycling.
“At Queen’s we take these pellets and grind them into a fine powder, which is then blended with a proportion of new plastic (polyethylene), heated to over 200ºC and then cooled within a mould to transform it into the shape of a new product.”
Dr Martin adds: “Our research involves testing to find the optimum combination of blending the plastics and processing conditions so that eventually Harlequin Manufacturing will be able to introduce a range of new rotomoulded products made largely from post-consumer waste.
“It is expected that in one product of this kind waste plastic could replace around 30 per cent of the new plastic required and use the equivalent of 1,000 old milk bottles in its manufacture.”
At present, the UK rotational moulding industry alone consumes more than 38,000 tonnes of new plastic, of which more than 11,000 tonnes could be saved.
Mark Kearns, Moulding Research Manager at PPRC at Queen’s, added: “The rotational moulding process is unique in comparison to other plastic forming methods since it is used to manufacture large products that typically use very large volumes of plastics.
“This new process will therefore have significant environmental benefits. The ability to condense and transform large volumes of recycled plastics into products designed to last many years will result in a substantial reduction in the amount of post-consumer waste going to landfill, rivers and the ocean.
“It will also help to reduce the quantity of pure polyethylene used in the process, ushering in a new and more sustainable era in the production of rotationally moulded plastics.”
Rotocycle is a £500,000 project funded by Innovate UK, which began in January 2019 and will last for two years.
Nick Cliffe, Interim Deputy Challenge Director of Smart Sustainable Plastic Packaging, at UK Research and Innovation, said: “Plastics have transformed modern world in many positive ways. Yet today we are increasingly conscious of the devastating damage plastic waste can inflict on our planet and the wellbeing of people and wildlife.
“The Plastics Research and Innovation Fund will help help address these vital issue and projects such as Rotocycle will play a key role in this global effort.”
Media
Media inquiries to Emma Gallagher at Queen’s University Communications Office T; +44 (0)28 9097 3087 E; emma.gallagher@qub.ac.uk